Digital sewing with networked production control
Dürkopp Adler GmbHIn the textile industry an important factor for companies manufacturing industrial textiles is worldwide networking and improved efficiency of production processes. Digitalized production is also a precondition for complex sewing applications and for real-time monitoring of manufacturing and quality.
Dürkopp Adler AG, the largest European manufacturer of industrial sewing technology, is a market leader in this area from two different perspectives: the new and further development of the sewing machines themselves and the innovative IoT platform QONDAC, with which not only machines made by Dürkopp Adler will be networked and maintained remotely in the future.
This enables a digitalization strategy through the networking of production processes with continuous data flow, also across international borders. By analysing the data obtained from the machines, preventative maintenance, productivity and quality can be improved significantly.
Dürkopp Adler sewing machines such as the M-TYPE Premium can be centrally configured using QONDAC. In addition to a QONDAC backend-server (QONDAC Cube) the new touch control panel Commander CSP with HD video support and HTML display plays an essential role.
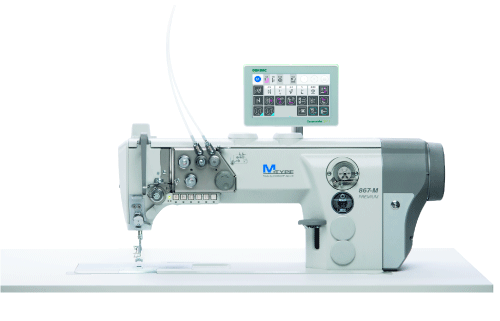
Software system for production networking
At the heart of this touch control panel is embedded-Linux-based Qt/C++ software with which, in addition to the actual operation and configuration, functions such as the remote updating of the machine software and diverse configuration parameters can be controlled.
The software consists of three components: a service application, which provides the maintenance technicians with user-friendly and secure access (Qt/C++, HTML5), a graphical user interface that resembles a typical smartphone screen and enables intuitive and thereby time-saving operation of the sewing machine, and a control application, which communicates with the machine-control systems of the sewing machine via various physical interfaces.
The parameterization of the machine and user profiles can be transmitted effortlessly; sewing programs can be updated reliably from the backend server. During the production process, material can be identified using a barcode scanner and the correct sewing program can easily be assigned. Production orders, for example in PDF format, can be displayed directly on the machine. Video tutorials that can be viewed on the machine as well as pre-configured setup programs additionally reduce the necessary learning time.
This software architecture is being used to follow a platform strategy: the Commander CSP is fundamentally compatible with very diverse machines in an innovative and growing product range. The software system was conceived right from the start to be scalable as the requirements grow. Existing control software and well-established legacy systems are integrated into the new architecture.
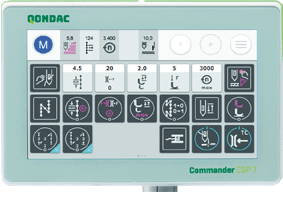
Investment security through scalability and variant management
In close cooperation with Dürkopp Adler, emlix was responsible for the software concept, the selection of the framework and planning the realization of the project. Hand in hand with the Dürkopp developers, emlix integrated the existing machine control system into the new software architecture and implemented the operation and service applications as well as the embedded Linux system as a basis. This included putting everything into operation on the hardware.
The essential functional requirements were thereby the vertical integration into the QONDAC network, NFC communication, scalability and efficient possibilities for customer-specific adaptations. The latter is very important for Dürkopp Adler as the spectrum of applications extends from the manufacture of vehicle seats via fashionable upholstered furniture to security-sensitive technical textiles, so that the M-TYPE machines must be flexibly configurable.
In addition to the software system, emlix provided the entire build infrastructure including defined processes for accurate management of the different machines and customer variants. In the medium term the developer team from Dürkopp Adler will be put in the position to take over the entire solution, to develop it further, to adapt it to customer requirements and to maintain it efficiently over its entire life cycle.
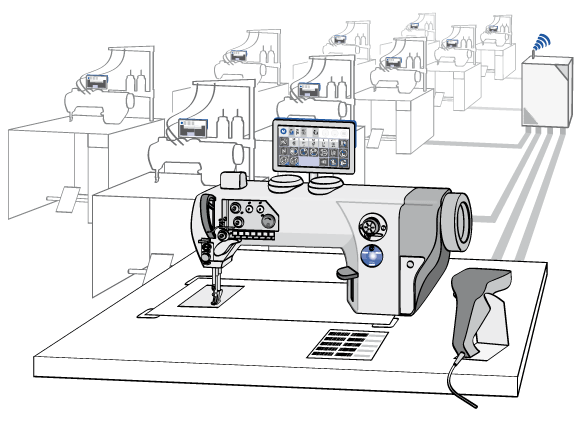